About Wiggers
Thanks to an excellent collaboration with our customers, we know and understand your challenges. This enables us to deliver solutions that perfectly match your needs and projects. Always ready for installation. By relocating the work from the construction site to our factory, we can conduct the entire production process under one roof. This enables us to get the most out of our machines and materials and we can provide customisation as well. This saves production steps, manpower and waste on location.
We will take you through our options in pre-processing, finishing, post-processing and delivery.
Pre-processing
All grinding, sawing and planing work is done in our own factory. This ensures a streamlined process and high-quality products. Our co-makers all have their own specialism and know the machines. This way, we create the profile you need, in the correct size. But you can also choose from previously completed or standard profiles.
Finishing: sheathing and veneering
Sheathing
All our products are sheathed: provided with a finishing layer. We use the material and look you want. This makes our products instant solutions. A couple of advantages at a glance:
- Seamless finish. Also in corners and on round details
- Consistent look. From the first to the last metre
- Any desired look is possible. This ensures your product always fits your project
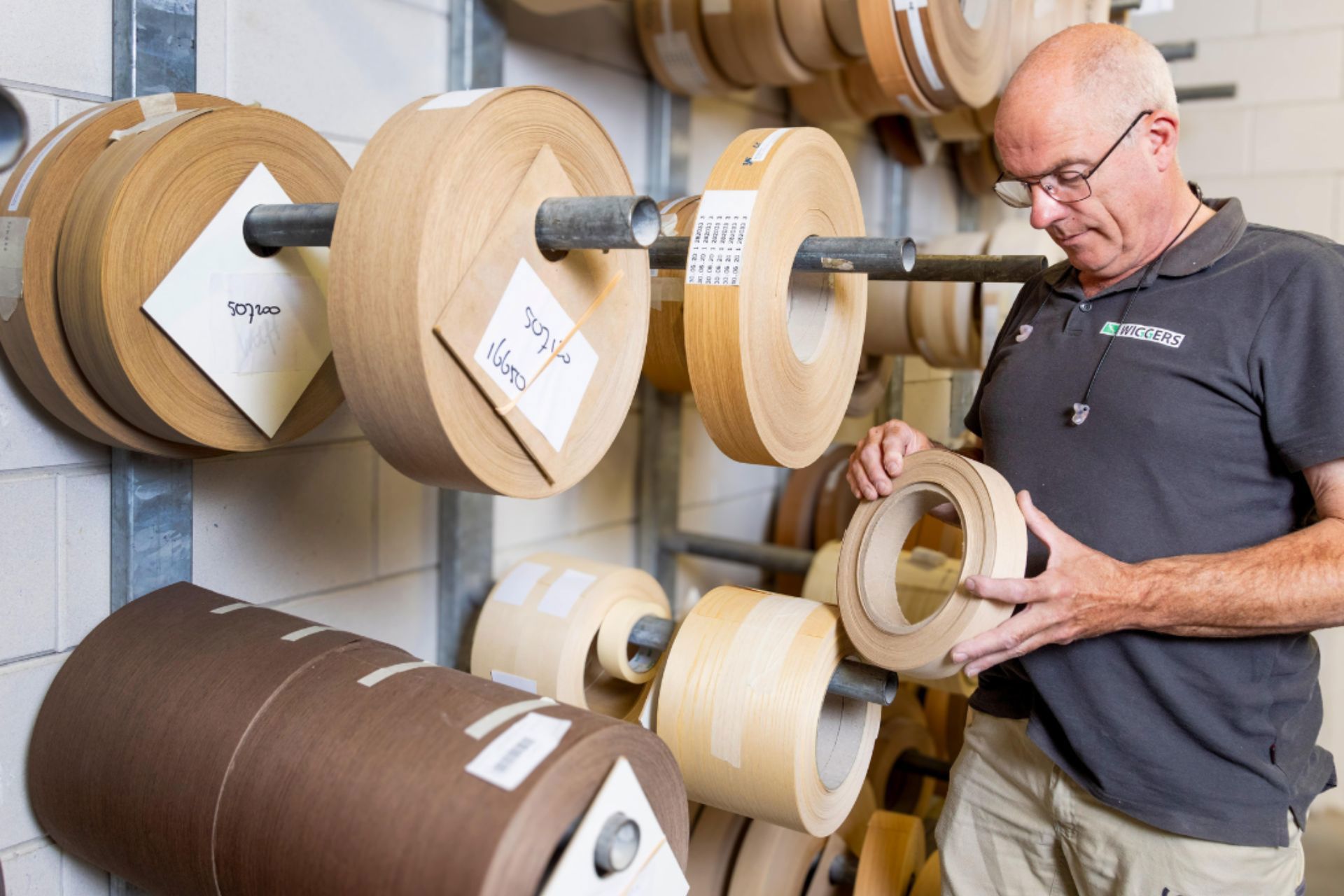
Veneering
Want the look of natural wood, without the disadvantages? We recommend opting for a veneer finish. This is a frequently used finish, especially in interior finishing and the furniture industry. The advantages of veneering:
- Consistent quality. No warping, cracking and/or splitting at long lengths as with solid wood
- Customisation. No high, costly failure rates
- A unique end product. Because we make veneer from real wood
- Varnished, oiled or stained veneer possible
- Fire-resistant impregnation possible (non-combustible, including A-test).
Post-processing
The possibilities of our post-processing are endless. Our machinery is designed in such a way that we can shorten, drill, mill, dowel, glue and install your product. Make it easy for yourself and use our co-makers for the most complete product possible.
Delivery
We pack all EcoProfiel products with a special foil to prevent damage. We can provide skirting boards with an adhesive strip and barcode. During packaging, we label the products and pallets as you wish. This makes it immediately clear on location which floor and room the products have to go to.
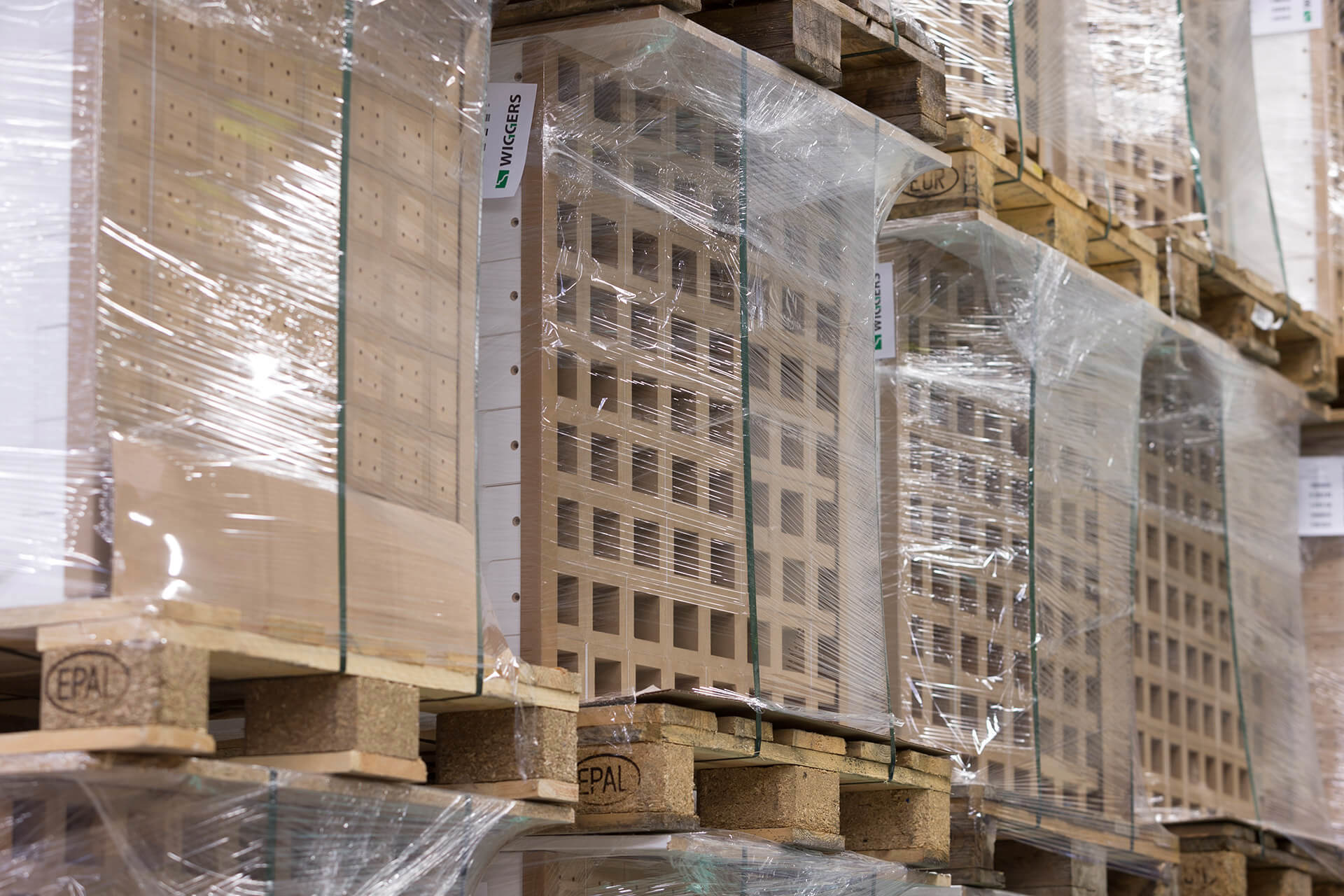
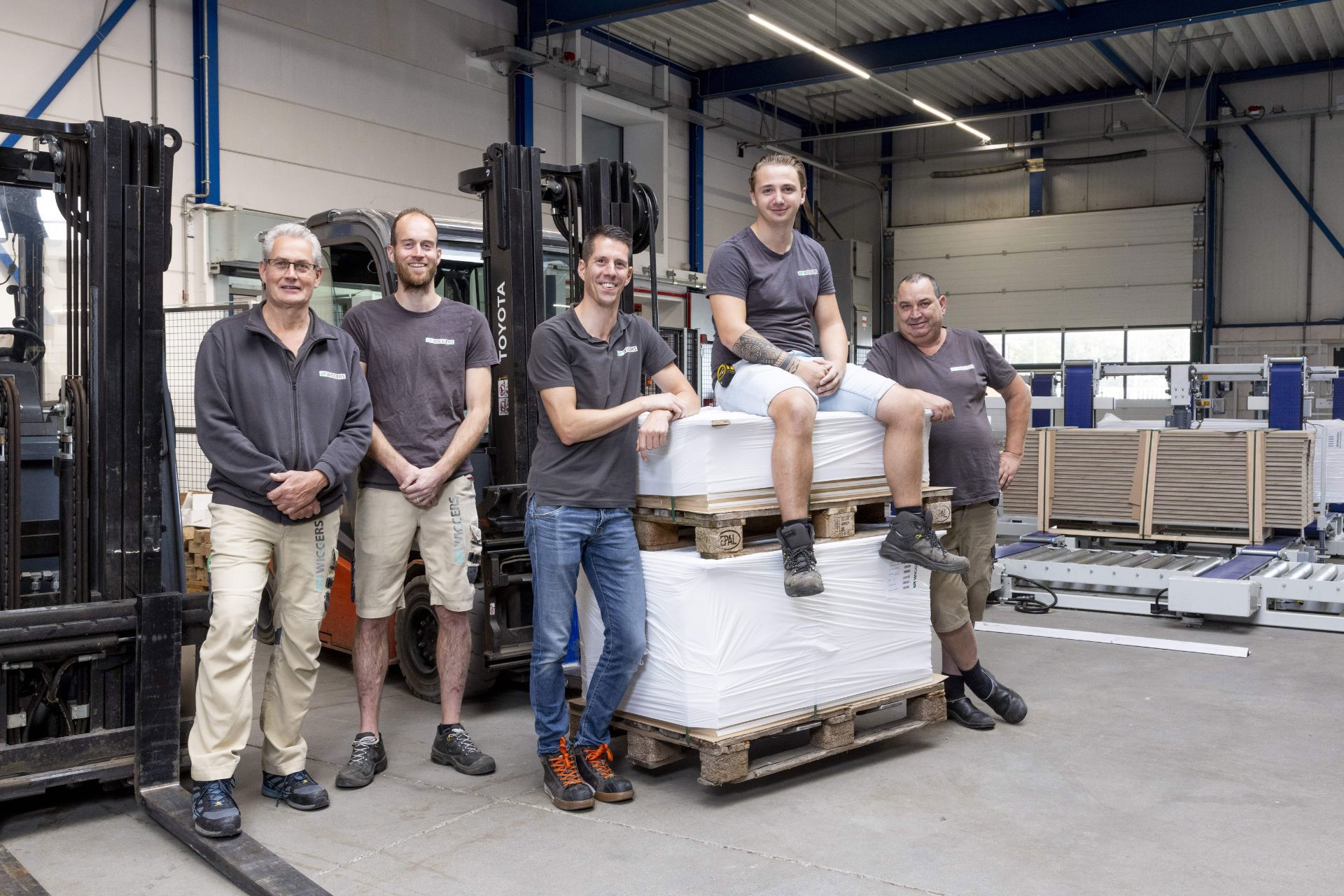
"Technological advances mean that the machines we work with are becoming increasingly sophisticated. This is interesting and offers more and more possibilities for the customer."
Roel Verwer
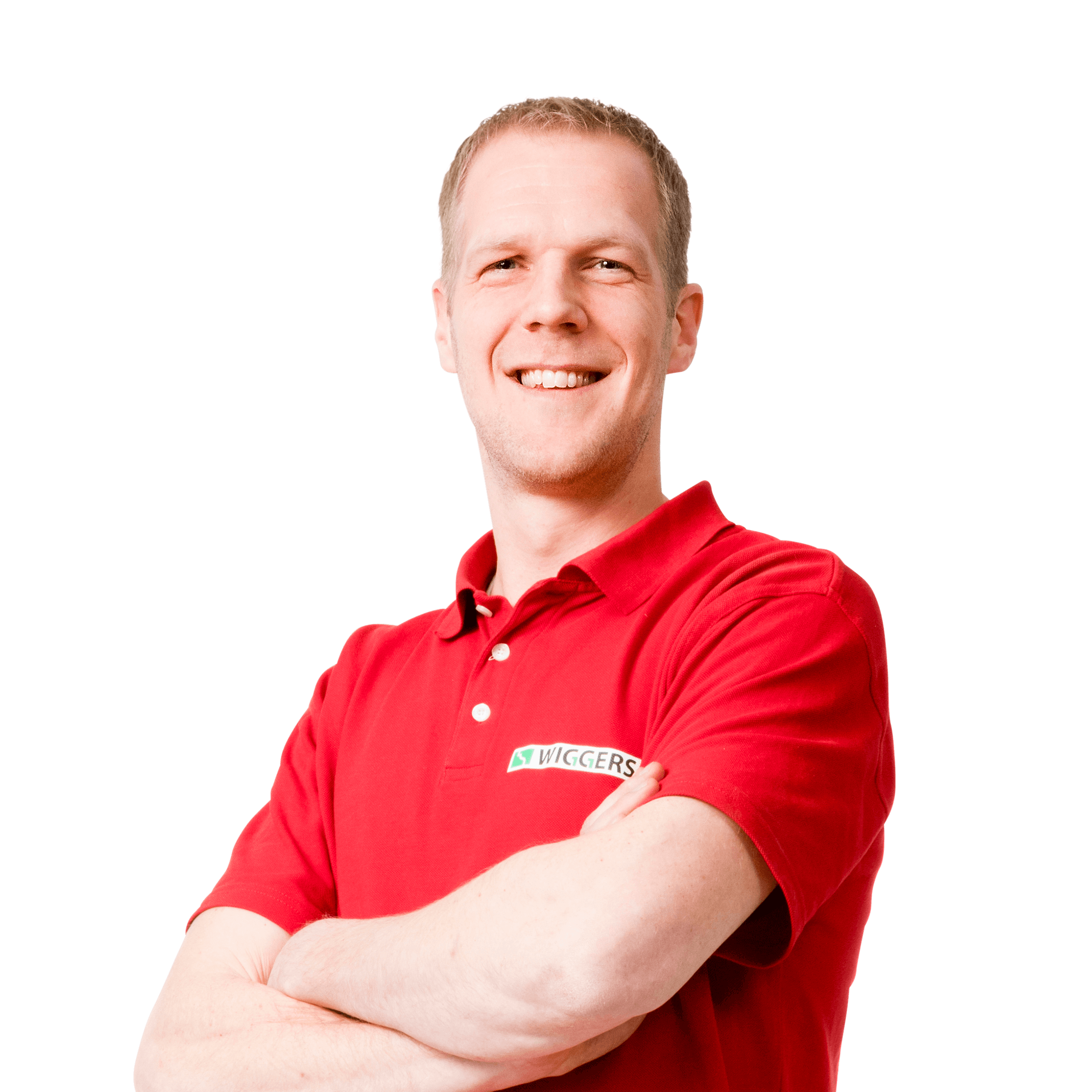
Product range covering material sheathing
Finishing with all RAL and NCS colours is possible. The most common covering material is melamine or plastic foil, paper and natural veneer. But we also handle the less obvious requests.
Range of veneers
With our extensive range of veneers, we serve the furniture, interior finishing, kitchen and luxury yacht building industries. Naturally, every type of wood is available in veneer. These are our most popular veneer finishes.
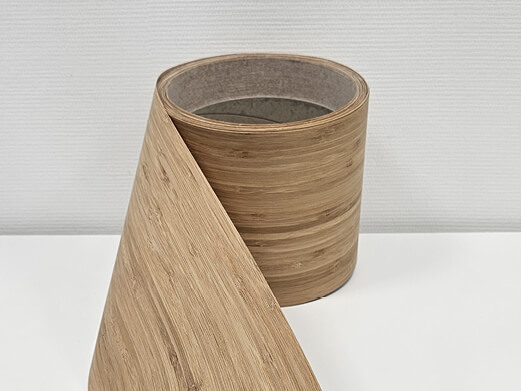
Bamboo Caramel
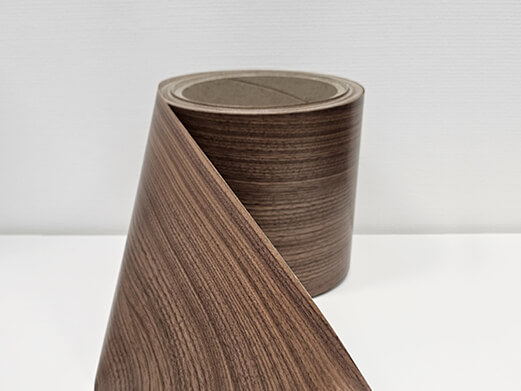
American walnut
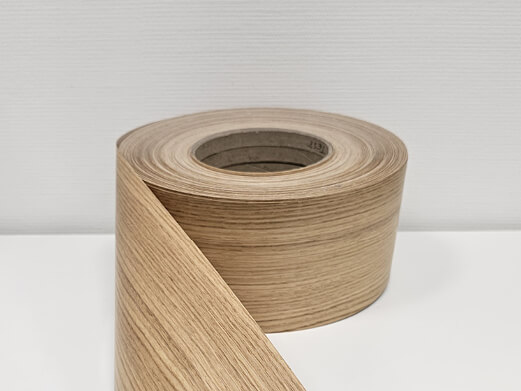
Oak
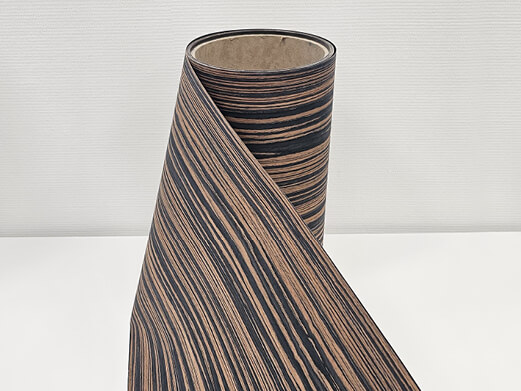
Engineered Wood
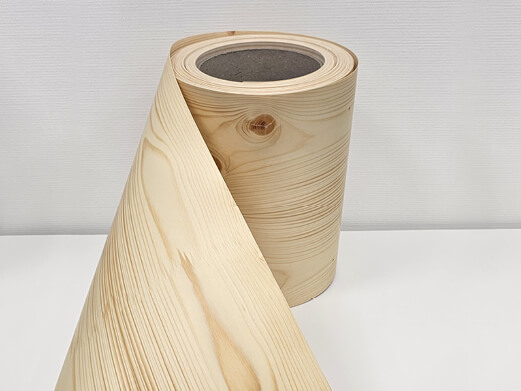
Deal
Cutting method
Natural veneer is cut to a thickness of 0.6mm, in 'booklets' of 24 sheets. The cutting method determines whether the resulting structure is quarter-sawn or bastard-sawn.
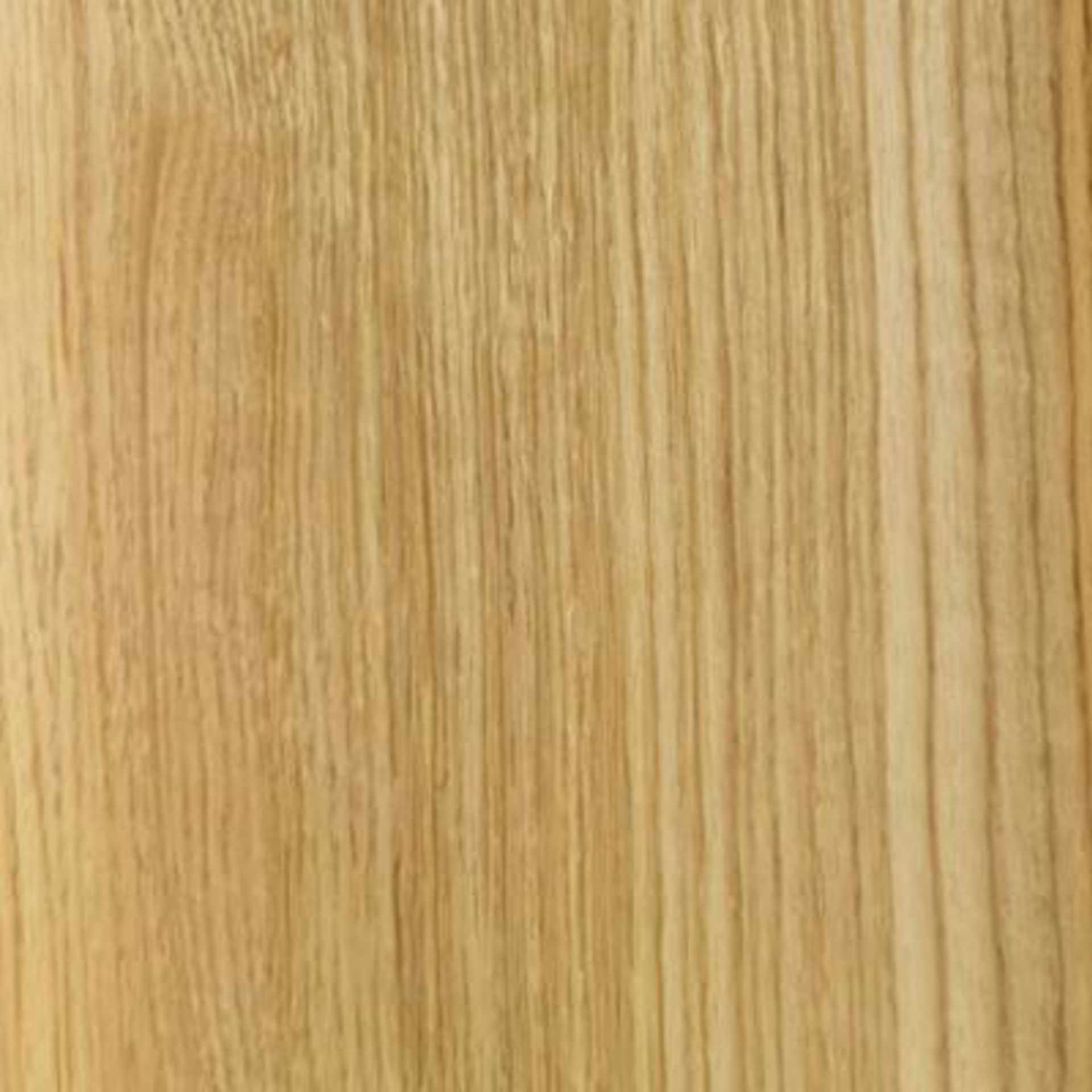
Quarter-sawn
Quarter-sawn is when you cut perpendicular to the annual rings. This gives a calm look with an even stripe pattern.

Bastard-sawn
Bastard-sawn is when you cut along the shape of the trunk. The annual rings are cut flat. This gives a more restless look with flame pattern. A combination of both is also possible.

Engineered wood
Engineered wood is an artificially produced veneer. Cut sheets are pressed together in a mould. They are cut diagonally. This creates a particular and very consistent structure.
Jointing techniques
Using modern technology and machines, the cut wood is processed into a veneer roll. It is up to you which technique we use.
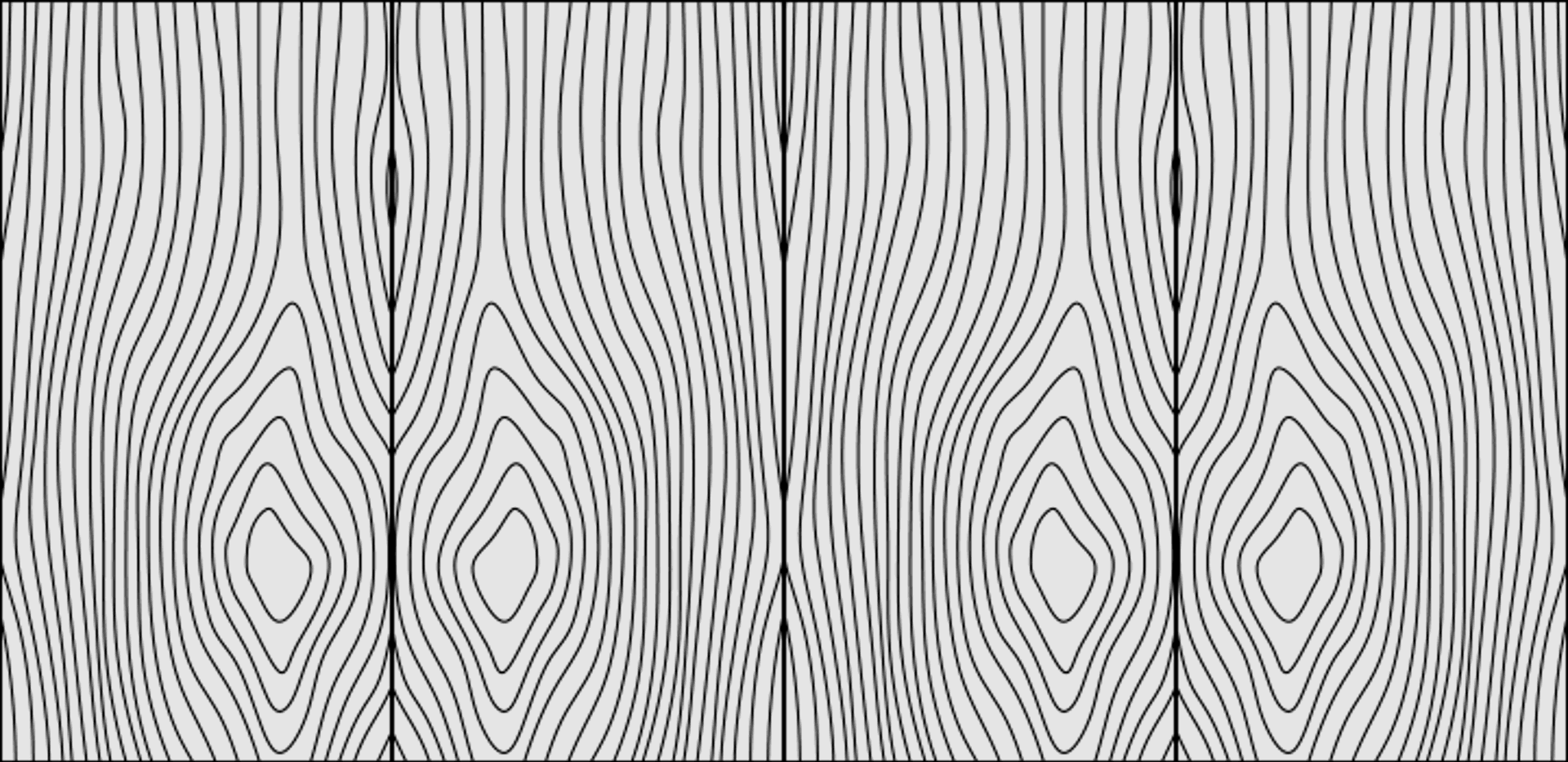
Book-matched
The sheets are glued in a mirrored manner, like the pages in a book. This technique makes the image variation of the tree clearly visible in the joined sheet.
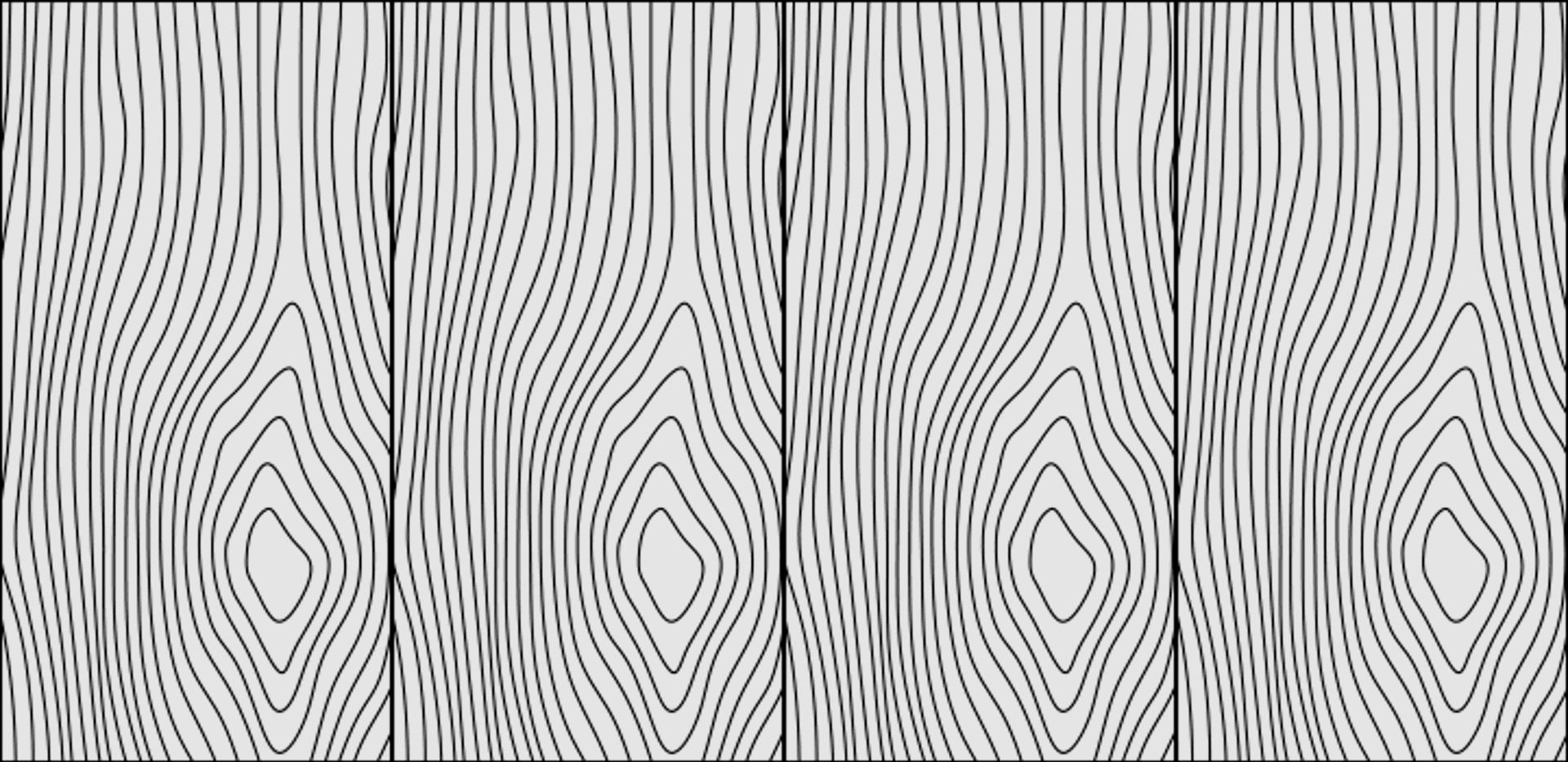
Slip-matched
The veneer strips have been slid off one after the other and joined together. This way, all the strips lie with the same side facing up.
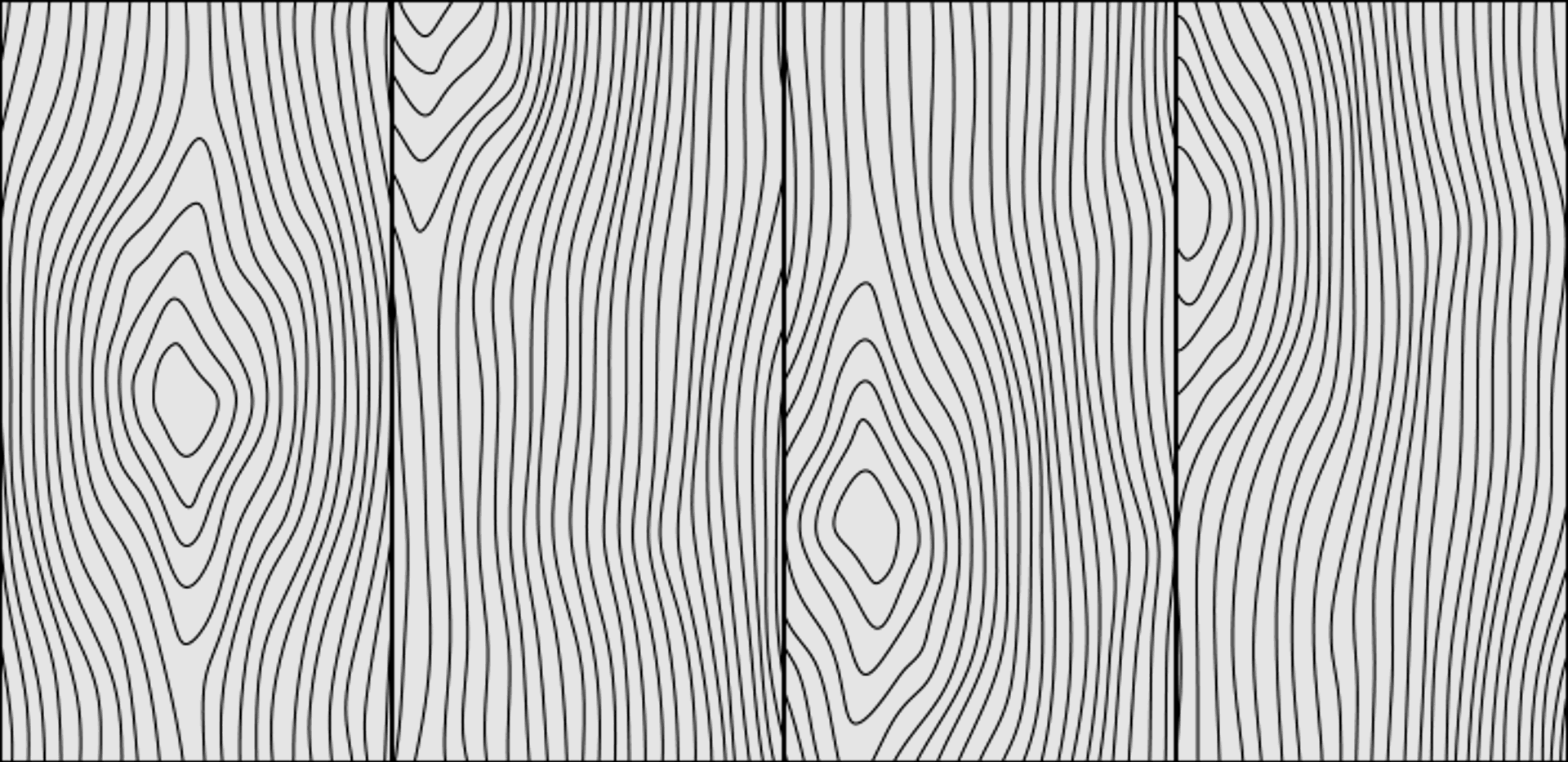
Miss-matched
A balanced design has been created by gluing and rotating the sheets.